Chattanooga Residents - Learn Lean Six Sigma’s History Here
Contact Us
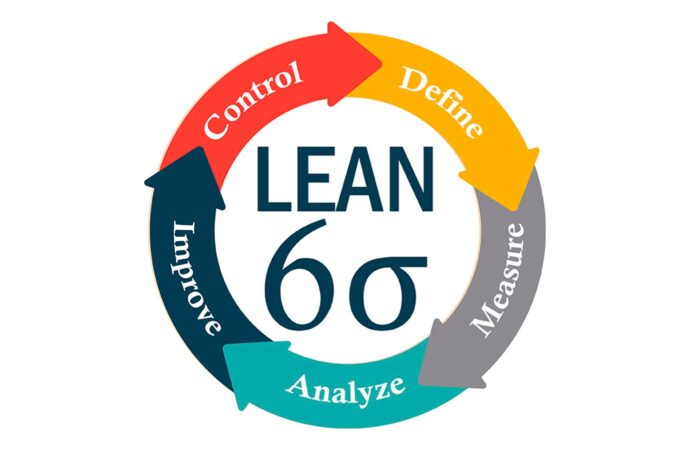
Lean Six Sigma has become a more common term and method, and many people are eager to implement it, but little do they know that studying some history will be needed to decide on doing it or not. Lean Six Sigma history is the cherry on top of the cake when you are learning how it works and whether this is a good option for your company. Thus, at Lean Six Sigma Curriculum for Chattanooga High School Students of Tennessee, we will make sure that you learn every detail, starting here!
To keep things simple, Lean Six Sigma is a combination of Japanese management principles and methods that can be traced back to the United States. Although it’s not Japanese, this topic can be complicated to discuss as some of the methods that originated in Japan back in the 40s and 60s influenced it.
Kaizen, which encourages cooperation and commitment as a means for continuous improvement, is the Japanese influence of the Lean Six Sigma methodology, at least the main one.
However, the main methods we need to remember are the Lean and Six Sigma methodologies as they were created before LSS—clearly—and contribute at their own levels without making LSS a simple combination or copy of them both.
But focusing on Kaizen for a minute is unique in that it emphasizes small, positive changes. Kaizen eliminates redundant steps and processes, which reduces time.
Many Japanese companies used and use this Japanese approach to increase their market share for their products, ideas, or services.
LSS can then be traced back to the USA, where it was created as a way to compete with Japanese industries. LSS was established in the 1980s to compete against super products, thanks to Kaizen and other process improvement methodologies.
How Did Lean & Six Sigma Start?
It is important to know the differences between Six Sigma and Lean. They are two distinct elements that were combined, and although they set the foundations for LSS, we mentioned the latter is not a simple copy of both.
Starting with Lean, because of its structure and principles, Lean is often called “thinking” since it emphasizes how a company should think about waste reduction and customer satisfaction while still handling other operations and goals.
Lean is tracked to Toyota and how it was included in the “Toyota Production System” (TPS). John Krafcik was a student of the former founder of Toyota. He was searching for a name that would describe the TPS system.
He wrote down the differences and characteristics between Toyota’s system versus traditional mass production on a whiteboard. After his research and analysis, he concluded that Toyota’s system requires less of everything in order to create value, which equals the entire concept of Lean at the time.
This whiteboard and conclusion quickly led to the Lean Thinking as result, and it set the basics: It focuses on reducing waste, non-value-added activities, and other areas.
Lean is built on its own principles and foundations. Understanding the customer is key to understanding each process’ value stream and waste, and although this feels similar to Kaizen, it is not the same.
Next, Six Sigma is an American-based methodology that dates back to the 1980s. Motorola is the original inventor of Six Sigma, and where we will focus this part of history.
Motorola had a hard time remaining a competitor to foreign companies in the early days. Its CEO Bob Galvin set a goal for a tenfold increase in five years.
This plan focused on global compatibility, participative management, quality improvement, and global competitiveness. Motorola quickly adopted six Sigma as the standard for all business processes since it proved to boost cycles and achieve better results.
Six Sigma was also taught to all Motorola employees. This ensured that everyone followed the same standards.
Both methodologies, taken together, recognize that change is the only way to go. Six Sigma is an excellent addition to the Lean approach. This is why LSS was created when they combined and set more principles from each of them and ensured results were maximized by setting the basics and following a pre-existing structure.
Then, How Does Lean Six Sigma Work?
LSS has been used in many different ways throughout history. It’s designed to improve productivity and efficiency and reduce waste.
Understanding the principles and solutions to Lean, Six Sigma, and Kaizen is a great idea. By doing so, you will be able to see the advantages and drawbacks associated with LSS.
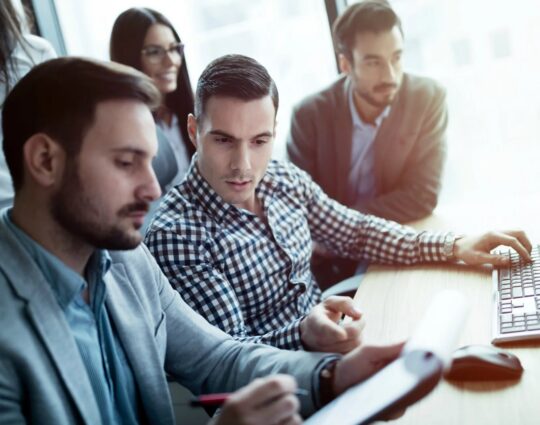
Lean allows employees and companies to better understand customers, prioritize their needs, and implement improvements. To achieve perfection, they can focus on the company’s value stream, processes, and value flow.
Six Sigma is dedicated to excellence and a system that promotes efficiency and clean operations. It is committed to continuous improvement and innovation in specific.
Kaizen is a five-part method that emphasizes customer satisfaction, teamwork, personal discipline, better morale, and quality circles. It also includes suggestions for improvement.
You can see the similarities between Six Sigma and Lean and how Kaizen affects the whole process by reading more about LSS and the entire concept of the final methodology.
Lean Six Sigma is a tool that can be used to benefit students and businesses equally for the previous reasons and how it was “built.” In short, you achieve this with the methodology is pretty much the same order:
- Learn how to reduce waste.
- Increase efficiency
- Reduce errors.
- Start taking less risk.
- Time management.
- Lower costs translate into higher revenues and better salaries.
- Motivate employees.
- Leadership and innovation are fundamental concepts and ideologies that get established in the company or person’s mind.
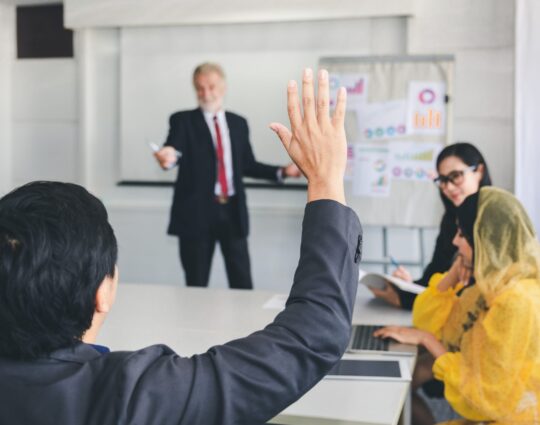
Lean Six Sigma Training in Chattanooga
Contact our Lean Six Sigma Curriculum Pros of Chattanooga team. We know the history and workings of the methodology head to foot. We are able to teach students in high school, college, all businesses, and whole companies how to incorporate LSS into their daily lives.
We want you to be a valuable asset in every place and company you decide to work in or for your own personal projects.